What is Porosity in Welding: Finest Practices for Preventing Porous Welds
What is Porosity in Welding: Finest Practices for Preventing Porous Welds
Blog Article
Comprehending Porosity in Welding: Checking Out Causes, Impacts, and Avoidance Techniques
Porosity in welding is a relentless challenge that can dramatically influence the quality and honesty of welds. As specialists in the welding market are well aware, recognizing the causes, results, and prevention strategies associated to porosity is vital for attaining robust and reliable welds. By delving right into the origin of porosity, examining its detrimental impacts on weld quality, and discovering reliable avoidance methods, welders can improve their expertise and skills to create top notch welds constantly. The complex interplay of variables adding to porosity needs a detailed understanding and a proactive method to make sure effective welding outcomes.
Usual Sources Of Porosity
Contamination, in the form of dust, oil, or rust on the welding surface area, develops gas pockets when warmed, leading to porosity in the weld. Incorrect shielding happens when the securing gas, typically made use of in processes like MIG and TIG welding, is incapable to completely protect the liquified weld pool from responding with the bordering air, resulting in gas entrapment and subsequent porosity. Furthermore, poor gas coverage, typically due to incorrect flow prices or nozzle positioning, can leave components of the weld unsafe, allowing porosity to form.
Impacts on Weld Top Quality
The presence of porosity in a weld can significantly compromise the overall quality and integrity of the welded joint. Porosity within a weld creates voids or dental caries that damage the framework, making it a lot more prone to splitting, rust, and mechanical failure.
Furthermore, porosity can hinder the performance of non-destructive screening (NDT) methods, making it challenging to detect various other flaws or stoppages within the weld. This can bring about considerable security concerns, particularly in crucial applications where the architectural honesty of the welded components is extremely important.

Prevention Techniques Review
Given the damaging influence of porosity on weld top quality, reliable avoidance strategies are crucial to maintaining the structural stability of welded joints. Furthermore, picking the appropriate welding parameters, such as voltage, current, and take a trip rate, can aid reduce the risk of porosity formation. By integrating these avoidance strategies right into welding methods, the incident of porosity can be considerably decreased, leading to more powerful and extra reliable bonded joints.
Relevance of Appropriate Shielding
Proper shielding in welding plays a crucial role in protecting against climatic contamination and making sure the stability of welded joints. Securing gases, such as argon, helium, or a blend of both, are commonly used to shield the weld pool from reacting with aspects airborne like oxygen and nitrogen. When these reactive components enter into call with the warm weld swimming pool, they can cause porosity, leading to weak welds with lowered mechanical homes.
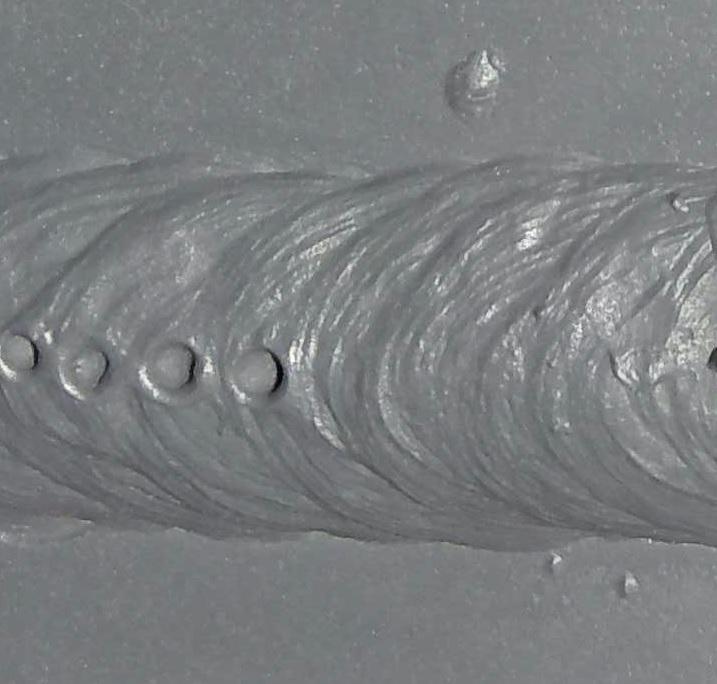
Insufficient shielding can lead to various flaws like porosity, spatter, and oxidation, compromising the architectural integrity of the welded joint. Adhering to proper protecting methods is necessary to generate premium welds with marginal issues and make certain the long life and integrity of the bonded components.
Monitoring and Control Techniques
Just how can welders properly check and regulate the welding process to make certain optimum outcomes and stop problems like porosity? By continually keeping an eye on these variables, welders can identify variances from the optimal problems and make immediate changes to prevent porosity development.

In addition, carrying out proper training programs for welders is vital more for checking and managing the welding procedure effectively. What is Porosity. Informing welders on the importance of keeping constant criteria, such as proper gas protecting and take a trip rate, can assist prevent porosity concerns. Regular assessments and qualifications can also guarantee that welders excel in monitoring and managing welding procedures
In addition, making use of automated welding systems can enhance tracking and control capabilities. These systems can specifically regulate welding criteria, lowering the likelihood of human error and making certain consistent weld top quality. By combining innovative monitoring innovations, training programs, and automated systems, welders can properly keep track of and control the welding process to decrease porosity defects and recommended you read accomplish why not find out more high-quality welds.
Final Thought
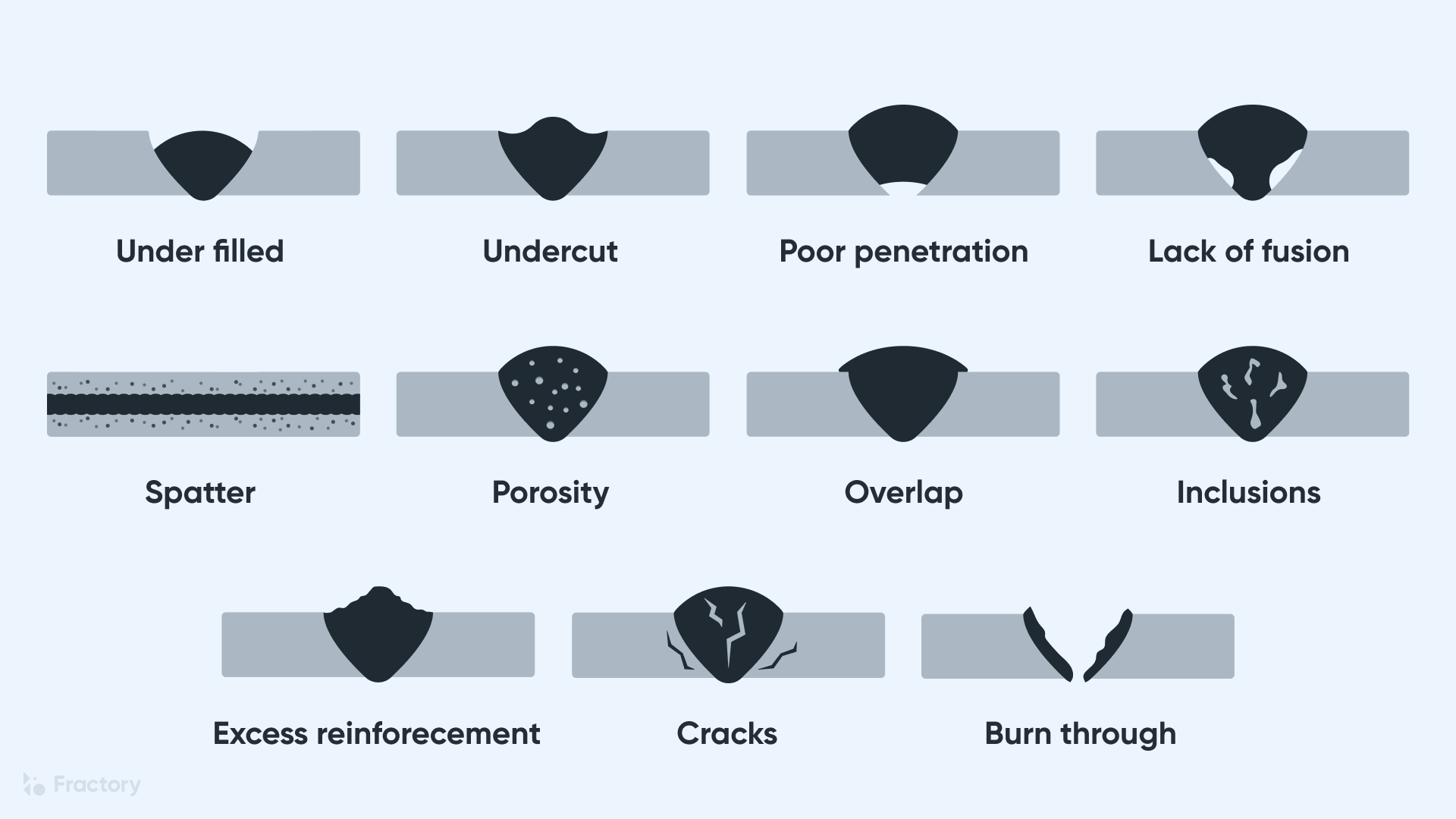
Report this page